|
|
Festina Lente: Hardtop
Am Anfang fand sich auf der Festina Lente eine Kuchenbude in stark reduziertem Zustand vor.
Fest montiert war eine rund gebogene Frontscheibe aus einer einzigen, ganzen Tafel aus 8mm Polycarbonatglas, die durch Alter komplett opak geworden und
mit Rissen durchsetzt war. Daran angesetzt ein Stoffzelt, an der Oberkante der Frontscheibe mit einer Kederschiene befestigt, dessen Nähte und Applikationen
in Auflösung begriffen waren. In jedem Fall stand eine Erneuerung an. Statt die alte Konstruktion einfach zu erneuern, entschied ich mich zu einem festen
Hardtop, nicht nur weil ich mehr Dauerhaftigkeit erwartete, sondern auch um bei schlechtem Wetter besser geschützt zu sein, und nicht zuletzt als Basis für
Solarpanels.
Nachteile der alten Kuchenbude:
- Nicht dauerhaft, stand nach nur 5 Saisons zur Erneuerung an. Die Risse in der Scheibe erschienen schon, bevor das Schiff im Wasser war.
- Nicht begehbar, zB. zum Reffen des Großsegels. Seefestigkeit zweifelhaft
- Außen keine Griffe zum Festhalten (Wichtig um bei schlechtem Wetter gefahrlos nach Vorne zu gelangen).
- Wärmestau, macht im Mittelmeerklima den Aufenthalt im Cockpit zur Tortur, auch wenn nach hinten alles offen ist.
- Der rückwärtige Verschluß kollidiert mit der Großschoot, zum Segeln ungeeignet.
- Selbst wenn die Frontscheibe noch Transparent ist, hat der Rudergänger nur sehr eingeschränkten Überblick, vor allem nach der Seite.
- Demontage der Frontscheibe schwierig, ist für einen Landtransport unbedingt erforderlich.
Die alte Kuchenbude hatte auch Vorteile:
- Vollständig verschließbar, wenigstens im Hafen/Winterlager, dadurch bleibt im Cockpit alles trocken und UV-geschützt, hat insbesondere den Holzteilen gut getan
- Eher leicht ab- und Aufzubauen, nur die Frontscheibe ist fest.
- Eher billig, vor allem, wenn man das in einem Billiglohnland machen läßt (Türkei)
Das Design
Nachdem erstmal ein Landtransport anstand, fiel der Entschluß
zur vollständigen Entfernung der alten Konstruktion eher leicht. Die Nachteile des
Betriebs ohne Cockpitschutz wurden sofort erkennbar. Die Fahrt im Sommer über die Binnenwasserstraßen in Frankreich war für den Rudergänger ohne Sonnenschutz eine
Tortur, zum Abgewöhnen. Im Weiteren, im November weiter über Rhein und Main ohne Regenschutz eher noch schlimmer. Dabei lernt man, was man wirklich braucht!
Das neue Hardtop sollte im Wesentlichen aus Laminat bestehen, könnte aus Polyester Laminat sein, weil ich aber schon umfangreich mit Epoxid-Harz gearbeitet
hatte, blieb ich dabei. Die höheren Kosten für Epoxid haben an den Gesamtkosten nur einen geringen Anteil, und es verarbeitet sich erheblich leichter und
ergibt ein besseres Ergebnis.
Das Konstrukt sollte sich organisch an das Schiff anpassen, also vor allem kein winkliches, eckiges, aufgesetztes, unpassendes Ding. Ich habe als Erstes versucht,
den Absichten des Konstrukteurs nachzuspüren (Holman&Pye), und meine, im Deckslayout schon das vollständige Hardtop genau vorgeprägt gefunden zu haben.
Mich verwundert sehr, daß Wauquiez diesen Gedanken nicht aufgegriffen hat, obgleich er offensichtlich klar zu erkennen ist, und das Hardtop nicht als Extra
angeboten hat!
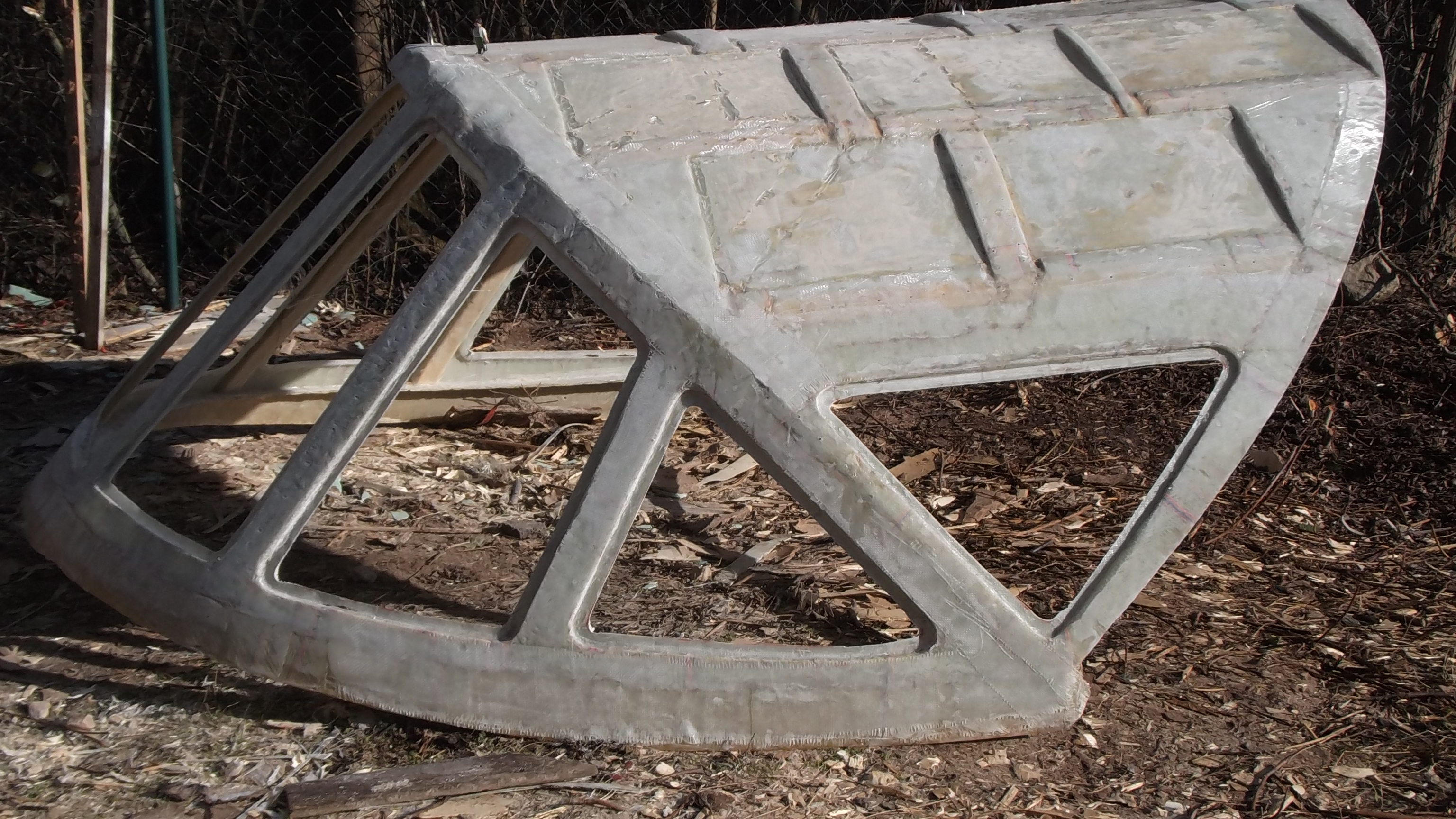
Dabei zeigt das Cockpitsüll ganz genau, wie weit das Hardtop reichen darf: bis zur hölzernen Verkleidung! Die Winkel, unter denen sich das Hardtop bis zum Dach
fortsetzt, sind ebenso vorgeprägt: Am hinteren Ende, wo die hölzerne Verkleidung beginnt, nahezu senkrecht, und ganz vorne in etwa einem 50° Winkel.
Die Scheitelhöhe korrespondiert mit der in der Kajüte vorgegebenen Stehhöhe. Nach hinten soll sich das Dach bis zum Rudergänger erstrecken, damit der noch
geschützt steht. Wie gut das vom Konstrukteur vorgegeben ist, erkennt man daran, daß der Winkel der hinteren Begrenzung des Hardtops in der Seitenansicht der
gleiche ist, wie auf der Vorderseite. Damit sind alle Eckwerte gegeben.
Das Fundament
Damit das Hardtop fest auf dem Cockpitsüll hält, und gleichzeitig leicht demontierbar1 ist, muß es formschlüssig auf dem Cockpitsüll
aufsitzen, und auf der Außenseite ein Stück überlappen.
Das erreicht man recht leicht und gleichzeitig genau, wenn das Fundament direkt auf das Cockpitsüll laminiert wird. Damit sich das Laminat nicht zu weit
ausbreitet, muß es sauber und rechtwinklig begrenzt werden. Hierzu habe ich einen 20mm PVC-Kabelkanal (ausreichend flexibel) mit demontierbarem doppelseitigem
Klebeband an der Außenseite des Cockpitsülls mit konstantem Abstand von 10cm von der Oberseite des Cockpitsülls befestigt. Man braucht dafür 4 Kabelkanäle a' 2m.
An der durchweg senkrechten Innenseite habe ich den Deckel eines 40mm Kabelkanals ebenso mit doppelseitigem Klebeband befestigt, so, daß der Streifen das
Cockpitsüll um etwa 10mm überragt.
Wenn nun die Begrenzungen fest und sicher, und auch dicht(!) plaziert sind, muß alles lückenlos mit reichlich Wachs isoliert werden, damit sich das Fundament
schadlos und rückstandsfrei vom Cockpitsüll lösen läßt. Isoliert und geschützt werden muß auch die weitere Umgebung, damit man vertropftes Harz wieder
entfernen kann.
Dann wird laminiert, wie üblich sparsam mit Harz, aber ohne Lufteinschlüsse! Die Dicke des Laminats sollte etwa 5mm an den Seiten betragen, auf der Oberseite
des Cockpitsülls etwa 10mm.
Wenn das Harz durchgehärtet ist (frühestens nach 24h, ist temperaturabhängig) Kann man (vorsichtigst) das Fundament vom Cockpitsüll abnehmen. Man wir sofort
erkennen, daß dieses große U-förmige Gebilde ziemlich schlapprig ist, und sich leicht verformt oder sogar bricht. Wenn das passiert ist, nochmal!
Man hebt es vorsichtig gerade soviel an, daß man an den Beiden Enden mittig der Sülloberseite etwa 20mm vom Ende ein 6mm Loch durchbohren, und dieses
Loch von unten(!) für eine 6mm Senkkopfschraube ansenken kann. Nach Plazierung dieser Schraube setzt man das Fundament wieder auf das Cockpitsüll zurück,
wo es sauber sitzen soll. Die beiden Schrauben an den Enden des Fundaments verbindet man mit einer Holzlatte fest. Die Bohrlöcher in der Latte müssen wirklich
ganz exakt zu den Schrauben passen, sodaß nach der Verschraubung das Fundament ohne jeden Verzug nach wie vor sauber und satt sitzt, nur durch das eigene Gewicht.
Diese Latte wird im weiteren den Verkehr im Cockpit erheblich behindern, ist aber unbedingt erforderlich und unverzichtbar, sie verleiht dem Fundament erheblich
mehr Stabilität und die wichtige sauber definierte Querdimension.
Diese Latte muß möglichst ohne Unterbrechung montiert bleiben, bis das Hardtop durch das Dach und insbesondere die achtere Griffleiste genügend Eigenstabilität
hat, auch wenn sie sehr hinderlich ist!
Die Frontseite
Nachdem die Vorderseite des Hardtops dem Winkel an der Außenseite des Cockpitsülls genau folgen soll, wird genau mittig eine
Holzlatte nach oben gerichtet, befestigt Hierzu wird das Fundament wieder angehoben und von innen(!) die Holzlatte mit einer 6mm Senkschraube außen
am Fundament befestigt. Für das untere Ende der Latte muß leider etwa 20mm über dem Deck ein Loch in das Cockpitsüll gebohrt werden, und die Latte
mit einer Laminatschraube und einer Abstandsscheibe, die der Laminatdicke entspricht, befestigt werden. (Später muß dieses Loch entweder zulaminiert
werden, oder mit einem Schraubstopfen verschlossen werden,)
Nun folgt diese Latte genau dem Außenwinkel des Cockpitsülls. Jetzt wird die Scheitelhöhe des Hardtops festgelegt. Ich habe das ohne Rigg und Großbaum
gemacht, aber offensichtlich genau gerechnet, des es blieb, wie beabsichtigt etwa 5cm Raum zwischen Hardtop und Großbaum. Gleichzeitig ergab sich für
die Stehhöhe soviel Spielraum, daß die Höhe unmittelbar vor der Bank, also nicht in der Mitte, die gleiche Höhe erreichte, wie in der Kajüte. Durch
das gewölbte Dach des Hardtops ist die Höhe mittig etwa 3cm mehr.
Der vordere Teil der Form
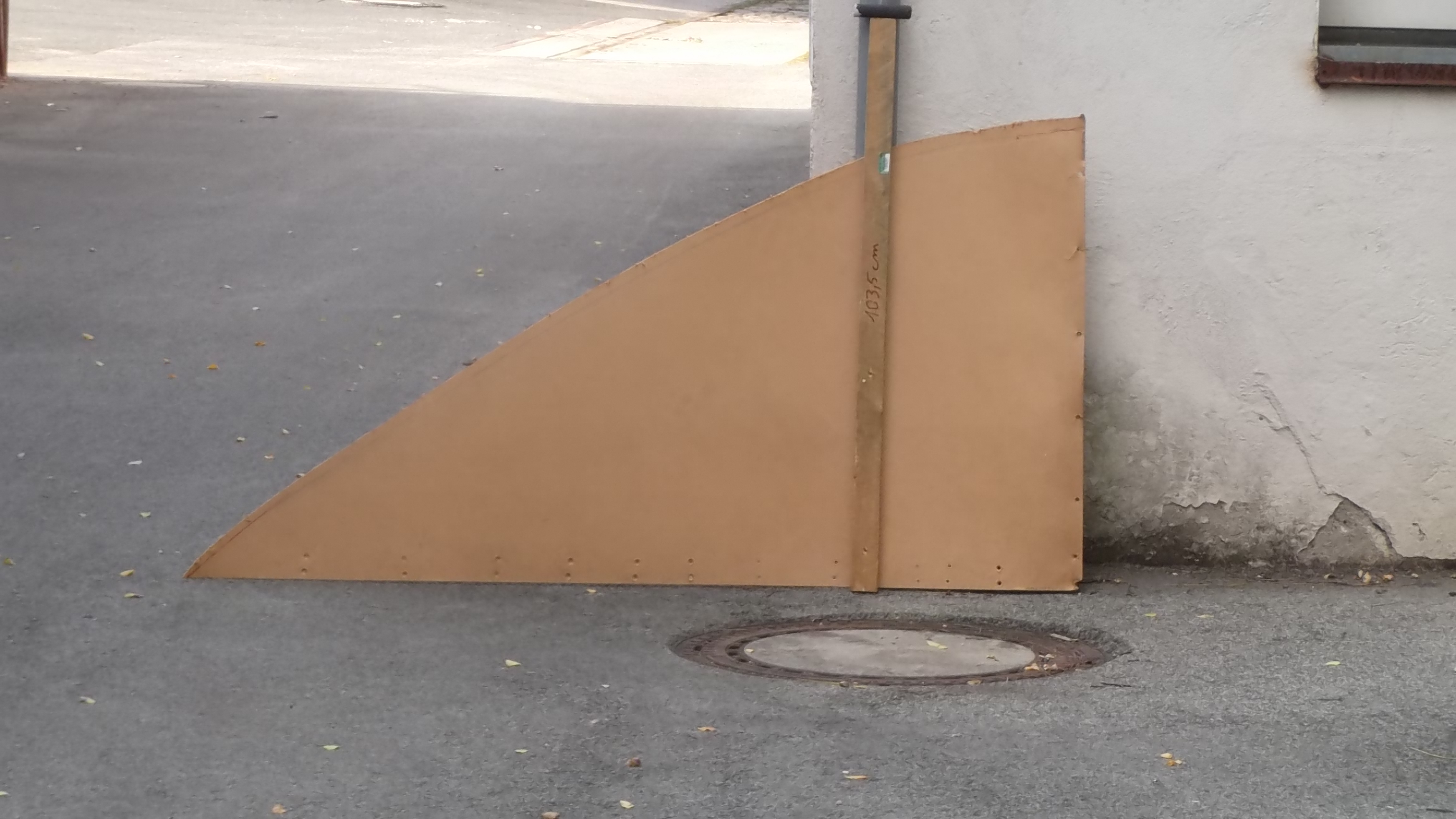
Die Form wird aus Hartfaserplatte (oder Dünn-MDF-Platte) hergestellt (Das Material, aus dem Rückwände von Schränken hergestellt werden).
Gibt es im Baumarkt in 2,4m*1,2m. Für die Vorderseite braucht man 2 Stck.
Im Bild sieht man eine Hälfte dieser Frontseite. Unten ist die originale Längskante der Platte, rechts die kurze Kante, beide im exakten rechten Winkel.
Entlang dieser Kante sieht man die Schraublöcher, mit denen das mit der Latte verschraubt war. Nicht im Bild das Gegenstück, das auf Stoß ebenfalls
mit der Latte verschraubt war. Man könnte diese beiden Teile auch aus einer einzigen MDF-Platte herstellen, wenn man das Foto als Schnittmuster nimmt.
Man demontiert die Latte von der Mitte der Vorderseite nochmal, und
verschraubt die beiden MDF-Platten mit ihrer Schmalseite auf Stoß, sodaß eine doppelt so breite Platte mit der Latte als Verbindung entsteht.
Zu beachten ist dabei, daß die glatte Seite der MDF-Platte auf die Unterseite der Form zu liegen kommt, und damit die Oberseite des Hardtops
bestimmt. Einbauten, die z.B der Stabilisierung dienen und NICHT im Hardtop abgebildet werden sollen wie etwa diese Latte, müssen auf der
Oberseite der Form auf der rauen Seite der MDF-Platte plaziert werden.
Diese auf die doppelte Breite vergößerte Platte ist etwas unhandlich, muß aber trotzdem auf das Schiff gebracht werden. Nun muß auf empirischem Weg
die Untere Kante an das Schiff angepaßt werden. Hierzu wird die mittige Latte wieder montiert. Die obere Kante der Platte bleibt unberührt, von der
unteren Kante schneidet man z.B. mit einer Stichsäge Stück für Stück weg, bis sich diese Platte an die Außenseite des Cockpitsülls anlegen läßt, ohne
mit dem Deck zu kollidieren. Man hat da eine gewisse Toleranz, die der Höhe des Cockpitsülls entspricht, man braucht jedoch eine Überlappung mit dem
Fundament, damit das (wieder von innen mit Senkkopfschrauben) mit dem Fundament fest verschraubt werden kann. Nach dieser Maßnahme muß das Fundament
wieder spielfrei und satt, nur durch das eigene Gewicht auf dem Cockpitsüll aufsitzen.
Die Oberkante bildet nun eine Gerade, die im Bogen von der holzverkleideten Stelle des Cockpitsülls zum Scheitelpunkt unter dem Großbaum und auf
die andere Seite des Cockpitsülls reicht. Dabei sorgt die Flexibilität der MDF-Platte für eine ausgeglichene Kurve. Diese ist keine der üblichen
mathematischen Kurven!, Kein Kreisbogen, keine Parabel, keine Hyperbel! Dennoch ist sie eindeutig durch das Deckslayout definiert!
Zur Sicherung wird diese zurechtgeschnittene Platte wiederum von unten mit Senkschrauben mit dem Fundament verbunden. Das Gebilde gewinnt damit
schonmal erheblich an Steifigkeit
Jetzt ist der früheste Zeitpunkt, das zum öffnende Fenster für die Mitte zu bestellen. Diese individuell angefertigten Luken haben eine lange Lieferzeit,
und es hat sich gezeigt das diese NICHT maßhaltig genau geliefert werden. Um den Platzhalter für das Fenster genau anfertigen zu können, muß das
Muster vorliegen. Alles andere führt zu Ungenauigkeiten, Nacharbeit, und möglicherweise zu einer kompletten Neuanfertigung!
Das Dach der Form
Nun wird der First festgelegt. Das vordere Ende ist durch den mittigen höchsten Punkt des Vorderteils bereits definiert, das hintere Ende ergibt sich einerseits aus der Horizontalen und einer
geraden Linie, ausgehend von dem hintersten Punkt der Vorderseite, die unter dem genau gleichen Winkel wie die Vorderseite zum First strebt. In der
Seitenansicht ergibt sich ein Parallelogramm.
Der First wird genauso mit einer Holzlatte festgelegt, die Vorne (an der Außenseite) mit der mittigen Latte an der Vorderseite Verbunden wird,
und hinten mit einer weiteren Latte an der Mitte der Querlatte abgestützt wird.
Diese Latte von der Mitte der Querlatte zur Firstlatte ist nicht senkrecht, sondern muß den gleichen Winkel zur Senkrechten haben wie die
Vorderseite der Form. Genau dieser Winkel ist im Deckslayout mit dem Winkel des Cockpitsülls in der Mitte vorne festgelegt.
Befestigt werden diese Latten aneinander an der Außenseite mit "Lochband"und Schrauben. Diese sind aus eher weichem Eisen und können passend
zurechtgebogen und abgeschnitten werden.
Nun kann erstmalig die Stehhöhe überprüft werden. Ausgehend von der Firstlatte muß noch die Dicke der MDF-Platte (3mm), die Dicke des Laminats (5mm),
sowie die Dicke der Einbauten für die Solarpanels (10mm) abgerechnetmwerden, um die wahre lichte Höhe vom Cockpitboden bis zum First (innen)
zu berechnen.
Zu bemerken ist hierzu, daß sich sozusagen die gleiche Stehhöhe wie im Salon nahezu zwangsweise ergibt, aber bis zum Großbaum noch etwa 10cm Spielraum
besteht. Da könnte man noch individuell variieren. Gleichzeitig wird man sehen, daß ein Rudergänger, hinter dem Rad stehend, vom Dach noch
abgedeckt wird, da also auch bei schlechtem Wetter ohne Ölzeug stehen kann. Leider gilt das nicht für die sitzende Position. Andererseits,
im wirklichen Seglerleben ausgiebig getestet, ist es leicht möglich, für den besseren Überblick auf die Sitzbank zu steigen, und über das
Hardtop hinwegzusehen, was nicht möglich wäre, wenn das Dach weiter nach hinten reichte.
Wenn das Großsegel gesetzt ist, ist der Großbaum nicht horizontal, sondern achtern etwas höher, sodaß der Rudergänger unter dem Baum hindurchsehen
kann, wenn er auf der Sitzbank steht. Aber Vorsicht!!!!, der Baum könnte dann bei einer Patenthalse den Rudergänger am Kopf treffen! Für diesen Fall
ist eine Baumbremse permanent installiert, die wenigstens die Folgen abmildert.
Wenn die Firstlatte nun genau nach der Längsachse des Schiffes ausgerichtet, horizontal und leidlich stabil verschraubt ist, und
nicht zuletzt die Frage nach der Stehhöhe positiv beantwortet ist, wird die Latte wieder demontiert. Auf einer glatten, ebenen Fläche werden
auf ihrer Unterseite mit der glatten Fläche nach unten 2 MDF-Platten mit ihrer Seitenfläche auf Stoß verschraubt.
Damit entsteht ein ziemlich großes,unhandliches, schlappriges Ding, das ohne Knick oder sonstige Verformungen wieder auf das Schiff gebracht werden
muß, die Latte mit den daran anhängenden MDF-Platten muß wieder exakt wie vorher als First montiert werden.
Wenn man nun die Platte vorsichtig bis zum Deck herunterbiegt, wird man sofort feststellen, daß die Platte viel zu groß ist. Man sägt nun auf
empirische Weise Stücke ab, bis sich das bis zum Cockpitsüll herunter biegen läßt. Dabei entsteht ein tunnelartiges Gebilde, das spannungsfrei auf der
Oberkante der Frontseite aufliegen soll. An der Hinterkante läßt man reichlich Überstand stehen, er stört zunächst nicht.
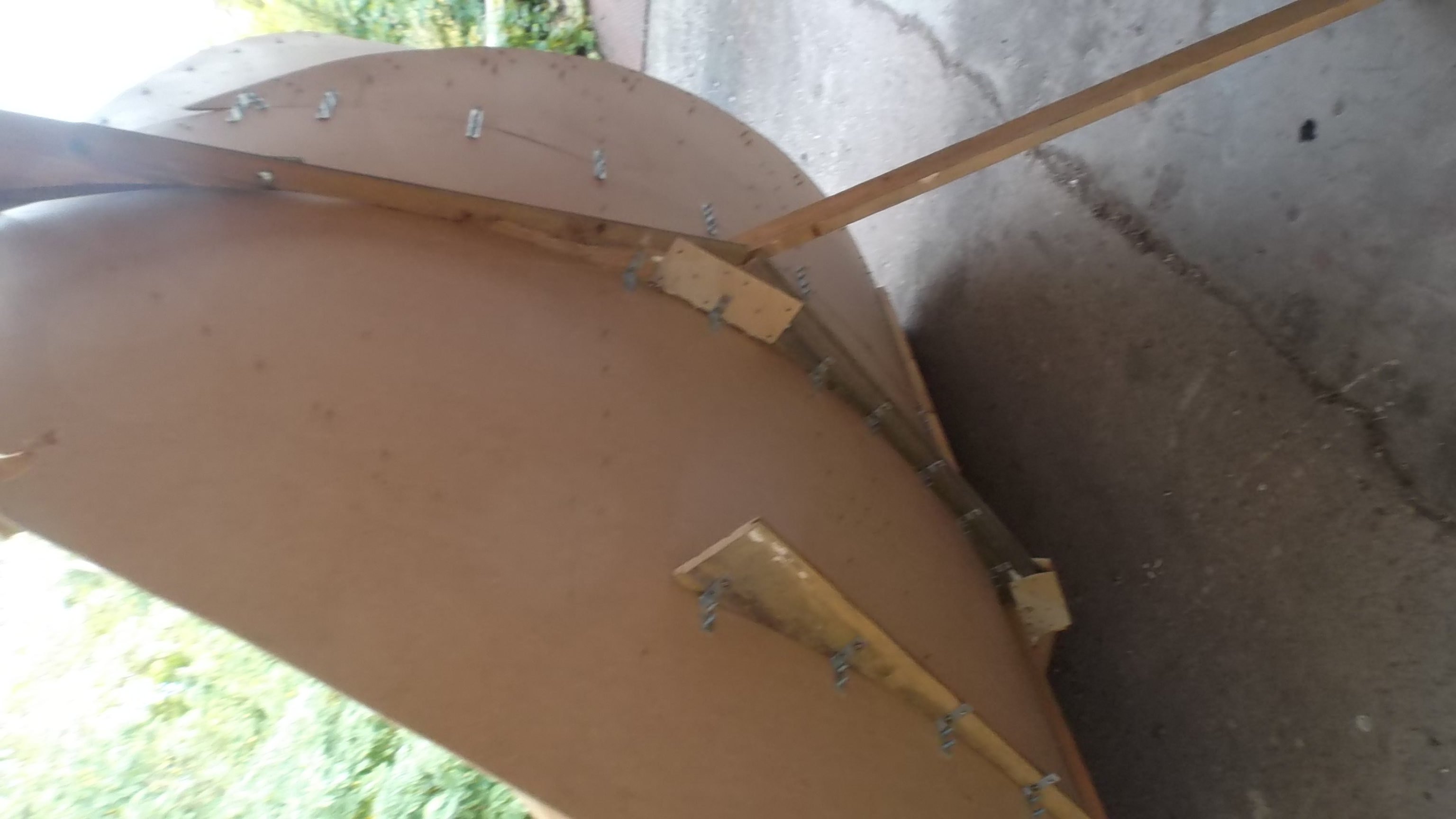
Nun ist Fein- und Formgefühl gefordert. Zwar wird die MDF-Platte schon eine Kurve bilden, aber analog zum Verlauf der Oberseite
des Frontteils ist das kein Tonnengewölbe! Tatsächlich ist das ausgehend vom seitlichen Cockpitsülle zunächst für die ersten 30cm eine nahezu
senkrechtstehende Gerade, die allmählich in eine zunehmende Krümmung übergeht, um im Firstbereich etwa einen Kreisbogen zu beschreiben. Ich habe
festgestellt, daß dieses Gebilde keinesfalls die nötige Stabilität hat, um während der weiteren Vorgänge, insbesondere des Laminierens, die Form
zu halten. Ich habe deshalb einen speziellen Außenrahmen angefertigt, der die MDF-Platte in der einmal gefundenen Form mit vielen Lochbandstücken festhält.
Besondere Vorteile des Hardtops
- Das Hardtop fügt sich organisch in die Linien des Schiffes ein
- Gegen jede Befürchtung ist das eine, zu öffnende Fenster völlig ausreichend, um auch im heißesten Mittelmeer-Sommer einen Hitzstau zu verhindern.
- Weder das Sitzen noch das Stehen unter dem Hardtop ist in irgendeiner Weise eingeschränkt.
- Die auf dem Dach installierten Solarpanels (13*20W Nennleistung) zeigten sich ausreichend. Insbesondere die spezielle Ausrichtun
zeigte sich effektiv. Es fehlt zwar eine mittägliche Spitzenleistung, dafür jedoch eine deutlich verlängerte Ladezeit, ohne daß die Ausrichtung
der Panels geändert werden müßte.
Nachträglich erkannte Nachteile und deren Behebung
Gestaltung der achteren Griffleiste
- Stärke des Griffwulstes
Materialien und Quellen
1 Zumindest in DE gibt es eine Höhenbeschränkung für Landtransporte. Die erste, eher leicht zu genehmigende Stufe ist eine Gesamthöhe von 4,30m.
Die Amphitrite43 unterschreitet diese Höhe (auf einem Spezialtransporter) ganz knapp, wenn alles auf dem Deck abgebaut ist, also Bugkorb, Heckkorb und vor allem
Hardtop.
|